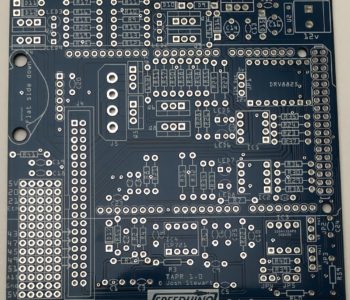
Quarinjection Selecting an ECU
At the beginning of the Quarinjection project, one of the major decisions was what ECU to use. There are only a handful of open-source ECUs that would make the cost feasible for the project. All the proprietary ECUs would cost the entire budget of the project.
RusEFI – Frankenstein, Frankenso, Prometheus, Proteus, Hellen…
These use SMD assembly which leads to a compact, clean board but is difficult to assemble. Based on the stm32f407 ARM development board and running ChibiOS/RT. Code is in C/C++ which is ideal as I have deep experience (not that there is any need to rewrite code).
Megasquirt
The first commercially available (2002) implementation of EFI using a microcontroller. Still sold, but built around on the older 68HC908 processor and the source code is not intended to open source. This has a different audience and there are many PnP versions for different cars. Only assembled boards and are 4-5x the cost of these others.
Speeduino
An interesting project for an open source EFI based on Arduino Mega. Less powerful than the stm32f407 which limits functionality and flexibility, but it should be good enough to work for this application. I’ve been doing quite a bit of Arduino (which is a wrapped C) lately and this is also comfortable.
I spent a few hours thinking about this and ultimately decided that the Speeduino BOM came out a bit cheaper and uses discrete components and the openness of both the platform and the software is attractive. And I already had an Arduino Mega clone in my parts box.
I bought a bare v0.4 board and VR conditioner from ebay (turns out it shipped from Israel) for <$15. It took about 2 months to arrive 🙁 after being lost once. I decided it was never going to arrive and ordered another board from a US supplier and… they both arrived a day apart.
I sourced components from my favorite new (to me) supplier: Mouser Electronics. Occasionally they don’t have something I’m looking for that are peripheral to core electronics (like Diametric magnets) but everything has been easy to find and compare, shipping is instant and customer service is great. Digikey is good also and they are my fallback. I think the BOM, including $14 of extraneous R&D components for my rainy day shelf came to $100.
I don’t know why, perhaps a return to my youth of assembling RadioShack kits, but I find assembling electronics very calming and satisfying. I savored the build of the Speeduino board. Here it is complete with the VR (variable reluctance) driver board for the cam/crank sensors and the stepper motor driver for idle control (which won’t be used in the initial build). I don’t know why some of the resistors spec’d are oversized (the brown blobby things) but I made them fit as well as possible. The Speeduino is just an Arduino ‘hat’ and underneath this board (you can see the pin outline) is an Arduino Mega clone. J5 is a high-amp output which I did not put a connector on yet because I’m not sure I’ll use it.
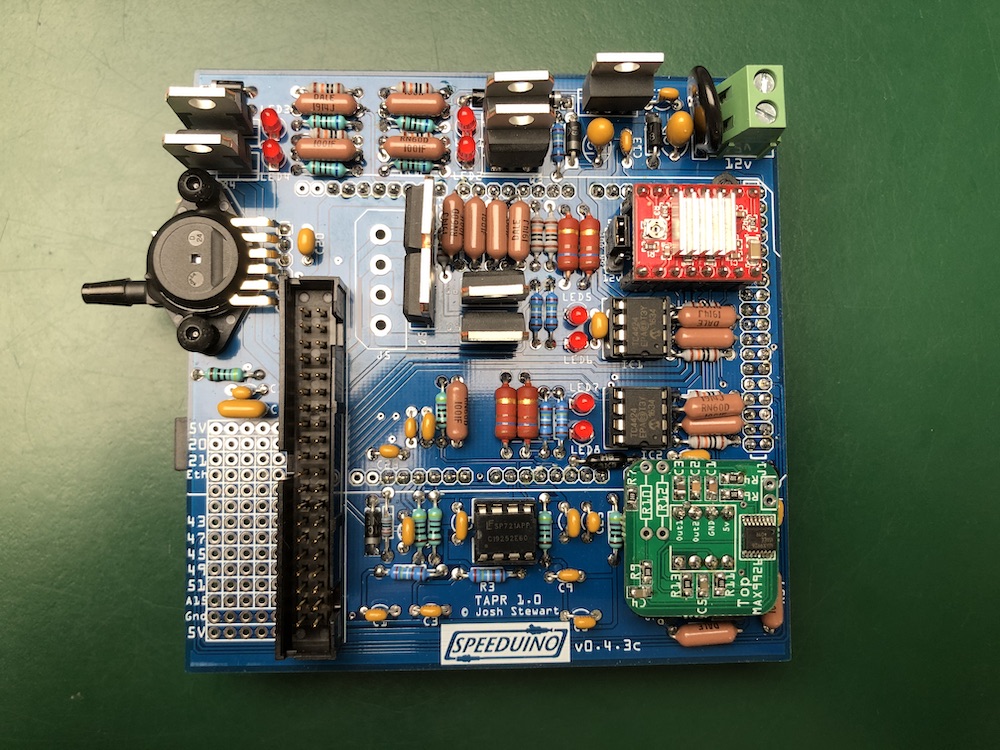